The deliverables of 3D scanning and reverse engineering can vary depending on the project’s requirements and end applications. In this blog, we will explore the various deliverables of 3D scanning and Reverse engineering with their use cases.
PointCloud
Point cloud data is a common output of laser and LIDAR scanning techniques. It consists of a collection of XYZ coordinates that represent the spatial positions of points on a physical object. These points collectively form a detailed and accurate representation of the object’s shape and structure in a digital format.
Portable arms, LIDAR scanners, and DRONE-based lidar scanners produce the direct point cloud output that can be exported as.ASC ,.Obj and the below file formats
- Point clouds are directly used for 3D reverse engineering for manufacturing.
- Point clouds can be used to make Factory CAD modeling & scan to BIM modeling.
- Use 3D point cloud files for 3D inspection in metrology software.
- Point clouds assist in reconstructing crime scenes and take measurements for investigations and legal proceedings.
- Point clouds assist in studying landforms, geological features, and terrain changes over time.
Some sample images of Point Clouds
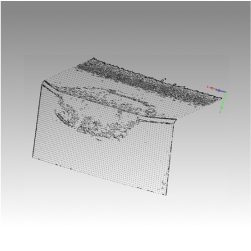
Point Cloud file deliverables from the software.
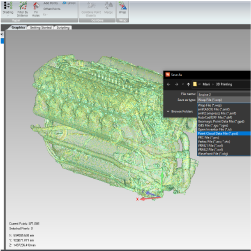
How Point cloud looks like this inside the software.
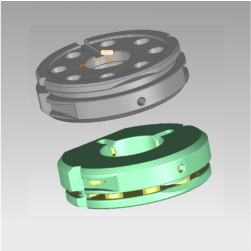
Complete set of merged point cloud.
Mesh Models
Mesh models are generated by converting point cloud data into a surface mesh composed of triangles or other polygonal shapes. These mesh models are commonly utilised for visualisation, analysis, and 3D printing purposes. However, it is important to note that mesh models are not ideal for design modifications or direct manufacturing. Making changes to mesh models can be challenging unless you have specialised sculpting tools like Geomagic Freeform. These tools enable more intricate modifications to the mesh model, allowing for design alterations and further manufacturing processes.Typically mesh models are exported as .STL files. Our 3D scanners directly deliver Mesh models in .stl file format.
Use cases
- Import into RE software for CAD modeling purposes.
- Use it with freeform or Digital Sculpting design software to enhance and modify organic shapes.
- Applications in 3D inspection and facilitation of 3D printing processes.
- Scanning and exporting of wood materials as mesh files, supporting wood carving manufacturing.
- Use the enclosed mesh model for accurate volume calculations across various domains.
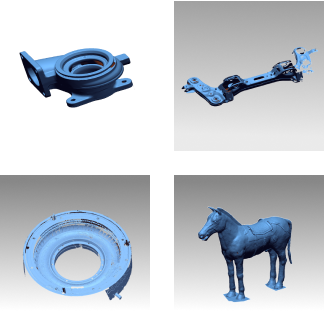
Some sample images of Point Clouds
Mesh models with texture
When the object is 3D scanned with texture using colour 3D scanners like Einscan , Faro Focus 3D Artec eva or any 3D scanners that have got the ability to 3D scan the colours , mesh models can be delivered with texture , below are the formats that support the textured mesh models.
Use cases of Mesh Models with Color Textures
- Use mesh models with colour textures to achieve vibrant and detailed 3D printed prototype products with accurate visual representations, aiding in design refinement before production.
- Facilitate the production of 3D characters, objects, and environments in movies and animations, advertising and marketing, enhancing visual storytelling and conveying concepts.
- Documenting and safeguarding cultural heritage sites, artefacts, and archaeological discoveries with accurate color representations.
- Supporting architects, designers, and engineers by providing detailed, visually rich representations of architectural and design concepts.
- Enriching video games with textured mesh models to create visually captivating environments and lifelike game elements.
- Applying textured mesh models to simulate fabric patterns and designs, assisting in virtual fashion showcases and design iterations.
- Enhance geospatial mapping by incorporating colour textures into terrain models, improving the visual interpretation of geographical data.
List of deliverables of Mesh model with texture :
- Wrap (*.wrp)
- 3D Studio (*.3ds)
- CTL (*.ctl)
- GeomView (*.oogl)
- ICF (*.icf)
- IGES (*.igs, *.iges)
- Keyshot (*.bip)
- Open Inventor (*.iv)
- OpenCTM (*.ctm)
- PLY (*.ply)
- PRC (*.prc)
- STL (ASCII) (*.stl)
- STL (binary) (*.stl)
- TWS (*.tws)
- VRML 1 (*.wrl)
- VRML 2 (*.wrl)
- Wavefront (*.obj)
Some sample images of Mesh model with texture

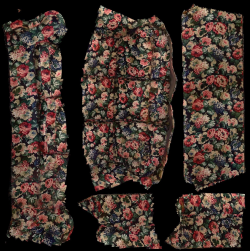
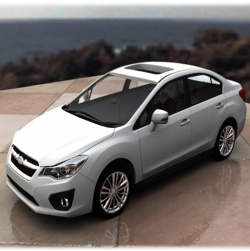
CAD Models In Neutral file formats
The final outcomes of the 3D scanning and reverse engineering process are CAD models. Specifically, history-based CAD models are crafted by utilising point cloud data or mesh models as references. This is accomplished through specialised reverse engineering software like Geomagic Design X. This software comes with a parametric feature tree, which allows these CAD models to be edited ,optimised and also employed
for manufacturing purposes.
Make Design Intent and As-built cad models in Geomagic Design X which are tailored to the specific applications they will ultimately serve.
When it comes to exporting these CAD models, they are exported in formats like IGES, STEP, SAT, and PS.
Use cases Reverse-Engineered CAD Models
- Integrate neutral CAD models into your CAM software, streamlining the manufacturing process by enabling direct translation from design to production.
- Enhance your design workflow by refining dump solids in your CAD system through reverse engineering, enabling comprehensive CAD mastering.
- Utilise reverse-engineered product CAD to create precise tool, die and mould designs, accelerating the manufacturing of complex components.
- Conduct package measurements using reverse-engineered CAD models, ensuring product compatibility and fit within specific packaging.
- Import reverse-engineered CAD models into CAE software for accurate simulation and analysis, aiding in optimizing product performance and structural integrity.
- Venture into the world of 3D printing by leveraging reverse-engineered CAD models, enabling the creation of physical prototypes and functional parts.
- Iterate and improve upon existing designs using reverse-engineered CAD models as a foundation, enabling efficient design modifications and upgrades.
- Create customised products by reverse-engineering CAD models and tailoring designs to individual preferences and requirements.
- Generate CAD models of existing components through reverse engineering, facilitating the production of aftermarket parts for maintenance and repair.
- Collaborate with cross-functional teams by utilising reverse-engineered CAD models as a common reference point, promoting effective communication and alignment.
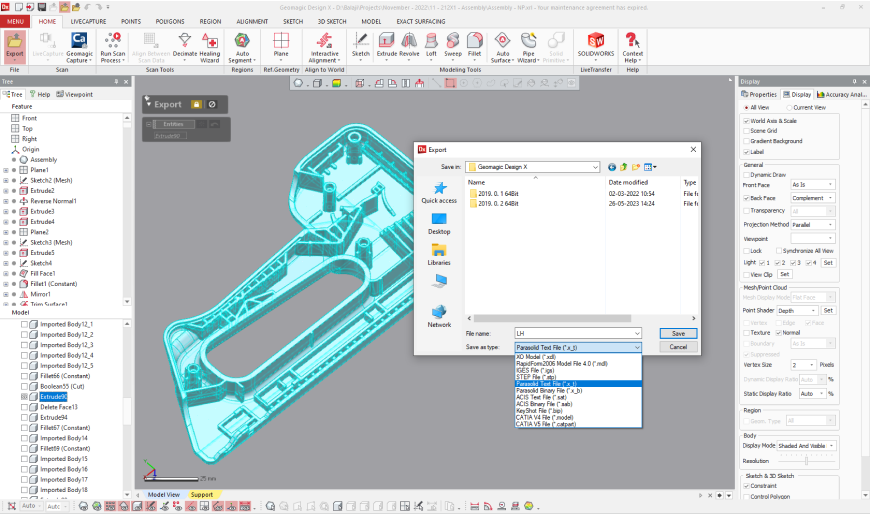
File format deliverable of CAD models in software interface
Sample images of CAD models
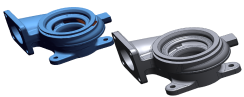
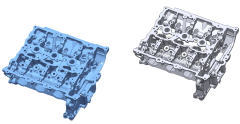
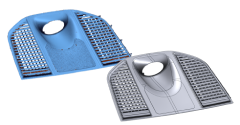
History based CAD models in CAD software formats (Live Transfer )
Sometimes, users may require a CAD model that possesses a fully editable history, allowing for convenient design modifications in their own CAD environment. To facilitate this process, the reverse engineering software Geomagic Design X offers a feature called “live transfer.” This functionality enables the seamless transfer of the entire modeling history to most CAD software in the market. Essentially, instead of using CAD software directly for reverse engineering, one can leverage the capabilities of reverse engineering software to perform scan-to-CAD operations. Subsequently, these features can be utilized to transfer the obtained data to the CAD model, ensuring that the output is editable within the user’s own CAD environment.
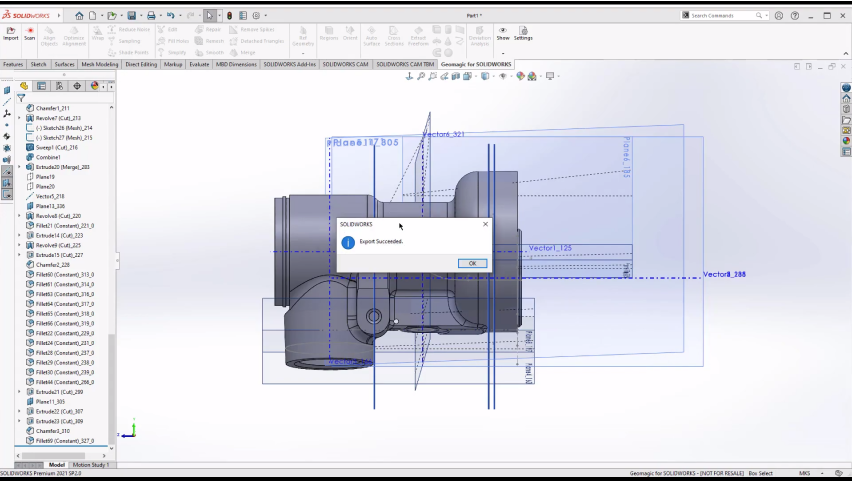
The outcomes of 3D scanning and reverse engineering can vary based on the project’s needs. This can include point cloud data, mesh models, as well as CAD models both in their native formats and within CAD software.
Leveraging these outcomes, engineers and designers have the opportunity to enhance their designs, cut down on development time and expenses, and ultimately create top-notch products that align with their customers’ requirements.
What's next ?
Enquire Now
As-Built Technique: In the as-built approach, we make sketches from the cross-sections that will be constrained to align
3D Reverse Engineering Workflow in Geomagic Design X Software
3D Reverse engineering is a 3D modelling process from the 3D scan that allows us to recreate
The deliverables of 3D scanning and reverse engineering can vary depending on the project’s requirements and end applications.
Unique Key features of Freescan Combo
Introduction: The Freescan Combo 3D scanner is an extraordinary device that combines the utmost metrology-grade precision with a